12月14日付で、朝日新聞より「造船業、幻と消えた5千億円 沈むか復権かの瀬戸際に」と題する記事が発表されました。
今回はその中で書かれていた「日本造船所の規模面での弱さ」についての解説を少ししたいと思います。
なお、はじめに商船の建造プロセスについて紹介しております。不要な方は目次より「日本造船所の規模面での弱さ」へ移行して下さい。
~お品書き~
造船業と設備
製造業というジャンルでは必ず製造設備が必要となります。もちろん規模の大小はあります。
自動車産業のような広大な工場を有している企業から、零細企業のように自宅兼工場のようなところもありますね。
さて、造船業における設備とは造船所内の各種設備となります。
船舶建造のプロセス
そもそも船舶の建造プロセスとはどういったものなのか。簡単にみてみましょう。
※より本格的に知りたい方には史上最強カラー図解 プロが教える船のすべてがわかる本や、建造以前のプロセスである営業活動から建造、そして解体までのすべてを網羅した船―引合から解船まで
をお勧めします。
さて、一部建造の流れを画像付きで紹介している造船企業があります。今回は新来島ドックに事業譲渡されたことで話題になったサノヤス造船を見ましょう。
地上艤装行程まで
船舶の設計と生産計画を建てた後、鋼材を入荷することとなります。
※実は日本で一番鋼材を使用する企業がトヨタ自動車で、2位が今治造船なのですよ!(鋼材使用量はトヨタに次ぐ2位、韓国と戦う瀬戸内の造船メーカー)。
その後、納入された鋼材をにさび止め塗装をしたり、切断していきます。それら鋼材を加工し、いわゆるブロック建造が可能なサイズまで組み立てます。
※ブロック建造とは、はじめから船台やドックで船底から積み上げて建造する方式ではなく、あらかじめ工場である程度船体を建造し、船台やドックで溶接して完成させる方式です。溶接技術の進歩により産まれた建造手法で、戦後日本造船業躍進の1つの要因でもあります。戦艦大和の遺産〈上〉 (講談社プラスアルファ文庫)の上下どちらかは忘れましたが、その当時のことについてよく書かれていますので、ぜひご覧ください)。
さて、この工場内でのブロック組み立て工程には小組立と大組立の2工程があります。なので、まだドックや船台での作業はありません。
造船の戦略としてはいかに早く船台やドックを開けるかが重要となってます。つまり、ブロックは大きければ大きいほど溶接作業が減少するので良いといえます。
ただし、ブロックをドックへ入れるためにはクレーンなどを利用しなければなりません。つまり、どれほどブロックが大きくても、それを持ち上げられるクレーンが力不足であればどうしようもないのです。このため、ブロック組み立てはクレーンなどの設備に制限されることとなります。
小組立は鋼材を切断し加工した鋼材を組み立てる段階で、家で言うと骨組みにあたる段階です。
(画像はサノヤスHPより。以下、特記なき場合は同出所)。
この小組立で完成したものをさらに組立るのが大組立の段階です。船体に近い存在になっていることが一目でわかりますね。
小組立、大組立を終えると、ブロックは工場からいったん外へ出されます。ここで、ブロック建造法と一緒に覚えていただきたいのが、先行艤装と呼ばれるものです。
つまり、ドックでの組み立て時ではなく、この段階で既に機器や配管などを取り付けておくのです。巨大な船内の入り組んだ閉所で作業を行うよりも、まだ小さなブロックの段階で艤装を施す方が安全で、生産効率も上がります。
※艤装とは、船の航海に必要となる装置や設備を設置することです。艤装と調べるとどうしても軍事よりの情報が多く出てきます。護衛艦なども主砲は進水後に搭載されます。商船や軍艦を問わず、先行艤装では配管の搭載など船体内作業の減らすための作業が多いですね。
船台、ドック、そして引き渡しへ
先行艤装が完了すると、いよいよ船舶を完成させる段階へ移行します。建造した船体ブロックをおもちゃのブロックのように積み上げていくのです。
画像で見てわかる通り、大型ブロックがクレーンで持ち上げられ、ドックへ搭載されていきます。サノヤスの門型クレーン(ゴライアスクレーン)は1基あたり800トンの能力を有しており、2基同時運用により1,600トンまでを吊り上げられます。
全てのブロックがドック内で溶接され、やっと進水式を迎えることとなります。新造用の船台やドックはあくまでも最終組み立てに必要なものであり、素早く次の建造船の為に開けないといけません。
そのため、ドック内作業はブロック組み立てに注力されるのです。進水後は岸壁に繋がれ、再び艤装行程に入ります。ここで船舶の最終的な形になっていきます。
次に海上試運転が行われ、性能通りか否かを見極めます。発注側の期待通りのスペックを発揮すると、いよいよ引き渡しとなります。
船舶建造における重要要因
簡単にみてきましたが、建造の流れはご理解いただけたでしょうか?本当に簡単な紹介ですので、より一層詳しく知りたい方は書籍などをご覧ください。
さて、船舶の建造に強く影響する要因として次のようなものが言えます。
船体ブロックの大きさ
船台やドックの回転率を上げるためには、一刻も早く船を進水差でなければなりません。そのためにはより大きなブロックを製造し、ドック内での作業数を減少させるのが一番です。
つまり、ブロックを持ち上げられるクレーンの能力が非常に大きな要因を占めます。
あるいは、ドック建造ではブロック製造専門の企業に大型ブロックを発注し、海上輸送して自社ドックへ引き込み、溶接して完成させる方法もありますね。
また、クレーンといっても造船は海に面しているのでクレーン船に頼ることも可能です。例えばIHIは3,600トンのつり上げ能力を有するクレーン船を販売してますね。
ドック数、規模
船舶建造数を増加させるためには、①ドック回転率を高くする、②ドック数自体を増やす、ことなどがあげられます。将来的に受注が見込めるならドック数を増やす投資を行うでしょうが、造船不況と呼ばれて久しい現在はドック回転率を上げることを優先しているといえます。
そもそも世界的に建造設備が過剰と言われている今、ドック新設を行う企業はかなり限られているといえます。国内での2000年以降のドック新設は、今治造船の西条工場と同社の丸亀新ドックくらいです。
「日本造船所の規模面での弱さ」
では、いよいよ本題へ入っていきましょう。今回の記事の元となった資料は国土交通省が発表した「造船業の現状と課題」です。
その中の「日本造船所の規模面での弱さ」と題されたページがこちらです。
今治とJMUは資本業務提携を発表しており、当初は2020年10月に営業設計の共同出資会社を設立する予定でした(今治造船・JMU連合、新会社設立を延期 21年1月に)。ただ、海外での独占禁止法などの審査により、来年への延期が決定しております。
仮に両社がグループ化した後のことを考えると、設備は数だけで見るとドック23基、船台2基という巨大なグループが誕生します。
一方で、韓国は現代が大宇を買収することを発表しており、実際2019年3月に合意が出ております。数だけで見るとドック23基に船台3基となり、これも巨大な存在になります。
※ちなみに、現代と大宇を合わせると世界シェアの2割を得ることとなります。また、中国国営2社も統合されることとなり、同じく世界シェアの2割を占めます。一方、今治とJMUは提携しても世界シェアの1割にとどまります。
注目すべきはドック数ではない
数の魔法と言いましょうか。造船所のドックの数だけで比較するのは決してやめてください。ほとんど無意味です。
図の左下に日本勢が集中している一方、中韓は右に集中しております。これは、造船所の事業所数によるところが大きいです。
今治造船はドック13基に船台1基とありますが、これをより深く見てみると瀬戸内を中心に5つの工場、6社のグループ企業から成ってます。つまり、造船所が散らばっているのです。
今治はまだしも、JMUは商船建造の拠点として有明、呉、津と日本各地に広がっており、とてもスケールメリットを受けることはできません。
※JMUは防衛関連として舞鶴、横浜(鶴見、磯子)に造船所があります。また修繕のみで因島に1つ造船所があります。
一方、現代重工は蔚山造船所がドック9基(執筆時現在は2基稼働中止で7基)となっており、グループ会社もドック4基やドック2基と船台1基のように、1つの造船所の規模が日本とは異なってます。
ただ、日本造船工業会の斎藤保会長(IHI相談役)は同有識者会議で「(造船所の)集約や構造改革には痛みが伴う」と訴えた(検証2020/造船再編 集約の波、艦船にも)とあるように、安易に統廃合をできない事情もまたあります。特に造船所は地方の一大産業であり、その周辺には関連産業も存在します。造船所の閉鎖は大量の解雇を伴うのみならず、再就職も県外へ行かざるを得ないなど多くの問題が発生します。まさに痛みを伴うのです。
※現代重工の郡山造船所(ドック1基のみ)が閉鎖された際、「市内の下請け企業の従業員約5000人の大半は失業することになる。下請け企業の数も一時の86社から現在では35社まで減少した。」という記事が出されてました。大げさかもしれませんが、事実として造船所閉鎖が雇用に大打撃を与えることに違いありません。
なぜ小規模は弱いのか
ここまでで日本型造船業は規模の小さな企業が多数存在していることを書いてきました。逆に中韓は規模の大きい企業が数社のみ存在しています。中韓の造船産業は集約化が進んでいるといえますね。
日本の他の産業、例えば海運などはかなり集約化が進み、今では日本郵船、商船三井、川崎汽船の3社がメジャーです(1964年以前は10社以上がひしめき合っていたのですよ)。
さて、規模が小さい事の問題ですが、調達コストはもちろん影響を受けることとなります。今治造船やJMUなどはグループで調達できますので、当然鋼材価格などは下がります。
他にも労働者の柔軟性や設備が分散されるデメリットもあります。人手が足りていたら不足しているところへ派遣するというのは、同じ造船所内では簡単ですが、数時間離れた造船所間では難しい。
その他、「同一事業所内に複数の大型船用施設はそれぞれを特定船種の専用ラインとして使用していることも指摘できる。。造船業の生産は経験工学的側面を強くもち習熟効果が高い」(麻生潤 造船大手企業の事業統合と建造設備より)等の効果もあります。
ただ、このような問題は正直それほど危機的な問題ではありません。最大のデメリットがロット受注に対応できないということです。
企業規模とロット受注
コンテナ船やLNG船は1隻1隻発注されるものではありません。一度に5隻以上の新造船をまとめて発注することをロット受注と呼び、2017年の世界受注量の38%がロット受注によるものでした(中韓勢の安値攻勢でピンチの“造船ニッポン”、政府対応待ったなし)。
実は、この数値の中に日本企業は存在しません。日本の受注は3隻以下が100%となっているのです。
もちろん、これは日本船主との強いつながりがあり、無理に受注する必要が無かったという理由もありますが、実際にロット受注できる企業それ自体が日本には少ないという問題がありました。
その代表例はカタール国営によるLNG船100隻以上の大量発注です。年間10隻のLNG船を連続建造するとして、韓国が大多数を受注したのです。日本にそれだけの建造ができる企業はありません。詳細は別記事をご覧ください(執筆時現在、ドック予約は済みましたが、本契約は先送りされてます。)。
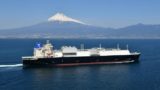
ドック規模で見る今治JMUと現代大宇
単にドックといってもその大きさは大小さまざまです。数の上で比較するのでなく、中型船までを建造できる設備なのか、超大型を建造できるのなかなどを見る必要があります。
※参考までに、船舶のサイズはVLCC(超大型原油運搬船)やQ-Max(カタールマックス)級LNGであれば長さ約340m、幅約60m、深さ約28mです。
今治JMU
今治造船は「船のデパート」と呼ばれるほど多種多彩な船種、大きさの船を建造してきました。それこそ世界最大級のコンテナ船を建造した一方でスモールハンディサイズのバルカーも建造します。
一方のJMUはその誕生がIHI、日立造船、JFE3社の造船海洋部門と住友の艦艇部門が合併して誕生したため、各地に造船所が散らばる結果になってます。ただ、ドックは上記3社が国策として行われた設備処理時に超大型設備を残す選択をしたため、いずれも大規模なものとなってます。
※今治造船HP 会社概要より。
※JMU 沿革・歩みより。
ドック規模
VLCC等の超大型船建造可能なドックはJMU5基と今治2基の計7基程度と言えます(あくまでも数値上であり、実際は不明です)。また、JMUは護衛艦などの官公庁船の建造と修繕も手掛けており、横浜の両工場や舞鶴などはそれに特化しております。一方の今治は新造に注力しております。それこそ、修繕ドックを埋め立てて新造ドックを建設したくらいです。
現代大宇(韓国造船海洋)
日本の造船業が古くから時代とともに発展してきたのと対照に、韓国はオイルショック後に急進的に成長を遂げました。その成長の要因の1つには、雇用を失った日本の造船関係者が多数韓国に渡り技術を教えたというのもありますが、オイルショック後に世界的に新造船設備を処理していた時期に、処理量以上に設備投資を行ったという韓国の国策もありました。
建造の主体はVLCCのような超大型船やLNG船、大型コンテナ船など高付加価値船に特化しているのも特徴で、そのため大型ドックが多くなってます。
※現代重工HP HHI_ShipbuildingBrochure_200421より。
ドック規模
※蔚山のNo4と5は2016年に稼働中止しています。また大宇造船の浮きドックは詳細不明です。
蔚山のドック9基が異常すぎて驚きますが、それ以外の造船所も新造船ドック4基など日本の造船所より多いことがわかります。また、日本で最大の造船所と呼ばれる三菱重工香焼工場は通称100万トンドックと呼ばれてますが、それと同等のものが3基現代にあります。
超大型船建造可能なドックは10基以上あるといえ、逆に中小型船に適している大きさのものはほとんどないといえます。
両国は建造船種も異なる
ドックを比較してきて今となって言うのもなんですが、実は両国は建造戦略が大きく異なります。
日本の建造船種
日本はオイルショックまで三菱や川重などの大手重工業系企業がVLCCを連続建造し、バルカーを今治や名村など中手が建造してきました。国内建造量の9割以上のシェアを大手が握っていた時代です。
オイルショック後、日本は国策として過剰な建造設備を削減することを決定します。その際に行われたのが「1社でも多くの企業を存続させる」という社会主義的な目的を有しており、結果、競争力の高い大手企業ほど処理量が多くなったのです。
※例えば三菱重工は総トン数5,000以上の船舶を建造可能な設備として7工場12船台2ドックを有していたが、2度の設備処理後は5工場4船台2ドックまで減少しました。このうちVLCC建造可能な設備はドック2基のみです。かなり長い歴史がありますから、ドックより船台が多いのが面白いですね。
そして、その後大手企業は三菱や川重のように特殊船やLNG船に特化する企業、住友のアフラマックスタンカー特化など高付加価値船に注力する方針を続けますが、規模の上で韓国や中国に勝てず、敗退していきます。
一方、中手はというと依然としてバルカーを中心に建造しており、中韓造船業がこぞって高付加価値船市場に注力したため、依然として市場で優位に立っております。低付加価値船と呼ばれるバルカーですが、だからこそ長い技術蓄積と国内で100%資材を調達できる造船関連産業の存在が大きく影響してますね。
韓国の建造船種
韓国は当初から産業の集約が進んでおり、現代重工、大宇造船、三星重工の3社で建造量の7割を占めるほどです(我が国造船産業のビジョンと戦略より)。本来的に造船業は低付加価値船の建造から始め高付加価値船へとシフトしていくはずですが、韓国はオイルショック後に高付加価値船へ特化する選択を取り、建造船種は今もその傾向が残っております。
もっとも有名なのはLNG船とコンテナ船で、その連続建造にはかなりの実績があります。特にコンテナ船は20フィートコンテナ(TEU)を何個積めるかで規模を表しますが、世界最大級のものは24,000級となってます。
※参考までに、HMMサンクトペテルブルクはコンテナを最大23,964個搭載できます。
2017年の日中韓受注船種
2017年1月から11月までのデータですが、月平均で日本は受注の約6割がバルカー、3割がタンカーとなってます。韓国はタンカーが5割を超え、コンテナ船が約3割です。ちなみに中国はバルカー、コンテナ、タンカーが各3割ずつです。
また、世界の船腹量における船種はバルカー、タンカー(オイルタンカー)、コンテナ船の3種で約7割を占めます。
※国土交通省 造船市場の現状 平成29年12月より。なお、同年の全世界受注量はバルカー28%、コンテナ11%、タンカー38%、LNG船4%、その他18%でした(国土交通省 造船業の現状と課題より)。
ロット発注はコンテナやLNGに多い
そして、ロット受注についてですがバルカーを大量に発注というのは少なく、多いのはコンテナやLNG船です。例えば、今治造船が受注したコンテナ船は2万個積みを11隻というものでした。LNGではカタール国営の120隻一括発注など記憶に新しいですね。
※今治造船HP 世界最大級20,000TEU型コンテナ運搬船 西条工場で竣工より。
参考までに、2017年のロット受注一覧が国土交通省より発表されてます(造船市場の現状平成29年12月)。コンテナやVLCCが多く、バルカーはVLOCほどの大きさの喪にしかありません。
今治造船はコンテナ船連続建造の為に、新たに丸亀に新ドックを建設する決定を下しました。残念ながら、それ以外の企業に新設はなく、丸亀新ドック以前の最新ドックは同社の西条工場でした。
今治造船の檜垣幸人社長自身が「国際的な受注競争に参加し、海運大手から一括発注をしてもらうには、超大型コンテナ船を年10隻程度は建造できる体制が必要」と話すように、ロット受注への対応は設備が無ければそもそも相手にされないのです。
終わりに
日本造船所の規模面での弱さという題でしたが、いかがだったでしょうか?
古くから続く日本の造船業は、必要な時に都度新設を行い、そのため各地に造船所が分散する結果となりました。これは欧州の造船業も辿ってきた歴史です。
一方の韓国は規模の経済を追求し、1つの造船所を巨大にする選択を行いました。日本という最新の事例をよく理解し、不足する技術は日本や欧州から引っ張ってきました。当然クレーンやCADなど最新の設備を調達できましたので、例えるなら日本は一気にタイムスリップしたかのような企業と競争することとなったのです。
1956年から世界最大の造船王国だった日本は2000年に韓国に抜かれ、そのわずか10年後に韓国は中国に抜かれました。
この中で、韓国の大宇造船は事実上の倒産し、WTO違反といえる莫大な公的資金が国からなされました。弱者淘汰の市場原理を大きくゆがめたことに違いありません。一方の日本は国からの支援が非常に少なく、コスト面でも苦戦を強いられる状態にあります。集約化が進まず、企業数が多すぎるという問題ももちろんありますが……。
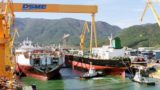
船なしには生きていけない日本にとって、造船産業は必要不可欠な存在です。それは生活の面でも、安全保障上の面でも言えます。
日本の造船産業が再び活性化することを願ってやみません。
それでは。
コメント